How to Manufacture Toilet Paper
Toilet paper is an essential household product with a steady global demand. The manufacturing process is a highly specialized and precise process, involving converting raw materials into soft, absorbent, and perforated rolls. The transformation requires a combination of natural resources, industrial machinery, and careful attention to quality. This article focus on the topic of how to manufacture toilet paper with a detailed step-by-step explanation, including sourcing raw materials, the production process, quality control as well as how to choose the right toilet paper manufacturer.
Raw Materials Preparation for Manufacturing Toilet Paper
The process begins with sourcing raw materials. This chart provides an overview main raw material for the toilet paper production.
Raw Material | Description | Common Uses |
Virgin Wood Pulp | Pulp derived from fresh wood, typically softwood (pine, spruce) and hardwood (birch, eucalyptus). Softwoods provide strength, while hardwoods contribute to smoothness and softness. | Main material for high-quality, soft toilet paper. |
Recycled Paper | Paper collected from post-consumer waste, such as newspapers, office paper, or cardboard. The paper is cleaned, de-inked, and processed into pulp. | Used for producing eco-friendly or lower-cost toilet paper. |
Bamboo Pulp | A sustainable alternative to wood pulp, made from bamboo plants. Bamboo grows quickly, making it an eco-friendly option. | Gaining popularity for eco-conscious toilet paper brands. |
Sugarcane Bagasse | Pulp made from the fibrous byproduct of sugarcane after juice extraction. It’s a renewable resource and a sustainable material for toilet paper. | Used for environmentally friendly, biodegradable toilet paper. |
Hemp Pulp | Derived from the hemp plant, which is fast-growing and sustainable. It’s durable, strong, and eco-friendly. | Often found in high-end or eco-friendly toilet paper. |

The Manufacturing Process of Toilet Paper
1. Pulping Process
The raw materials are turned into pulp through a process called pulping. This involves:
- Breaking down the fibers: Wood chips, recycled paper, or alternative fibers are mixed with water and chemicals in large vats called digesters.
- Heating and separating fibers: The mixture is heated, and chemicals break down the materials into a slurry of fine fibers and water.
- De-inking (for recycled paper): In the case of recycled paper, additional steps like de-inking are carried out to remove any leftover inks or contaminants.
The result is a clean, fibrous slurry that will form the base of the toilet paper.
2. Sheet Formation
Once the pulp is prepared, it is spread out on a moving mesh screen or a Fourdrinier machine. The steps involved in sheet formation are:
- Spreading the pulp: The slurry of pulp is spread evenly across a mesh wire, and water is drained away, leaving behind a wet mat of fibers.
- Pressing: This mat of fibers is then passed through a series of press rollers that squeeze out additional water, compacting the fibers together.
- Drying: The pressed sheet moves over large heated cylinders that dry out the remaining moisture, turning the wet fiber mat into a continuous sheet of paper.
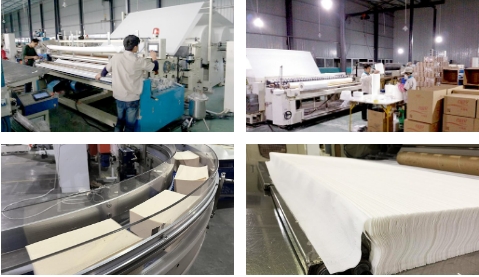
3. Rolling and Converting
Once the paper is dried, it is wound into parent rolls, which are large rolls of paper that can weigh hundreds of kilograms. These rolls are then fed into converting machines for further processing:
- Embossing: The paper is embossed with patterns to improve texture, softness, and strength. Embossing also makes the paper appear thicker.
- Perforation: A perforation machine creates small, evenly spaced holes to make it easy to tear the paper into individual sheets.
- Plies (if applicable): For multi-ply toilet paper, one or more layers are glued together to create two-ply or three-ply paper, which adds strength and comfort.
4. Cutting and Packaging Process
The large parent rolls are then cut into smaller rolls that fit the standard toilet paper size. Here’s how this part of the process works:
- Cutting: Automatic machines slice the large rolls into the desired size, producing individual toilet paper rolls.
- Wrapping: Each roll is wrapped in plastic or paper for protection and presentation.
- Packaging: The individual rolls are packed into bundles for retail sale. The packaging may also include branding, labels, and special eco-friendly wrappers depending on the brand’s marketing.
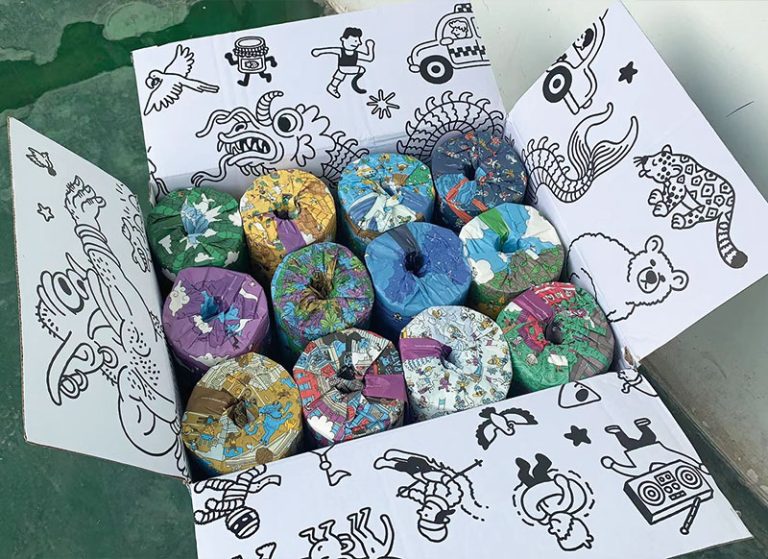
Quality Control in Manufacturing Toilet Paper
Quality control is a critical in the toilet paper manufacturing process, ensuring that the final product meets the required standards of softness, strength, absorbency, and hygiene. Quality control checks are performed at various stages of the production process to guarantee that each roll of toilet paper is both functional and comfortable for consumers.
1. Raw Material Quality Control
The quality control process begins with the selection of raw materials. These materials include virgin pulp (softwood and hardwood), recycled paper, and alternative fibers such as bamboo or sugarcane bagasse. The primary focus at this stage is:
- Cleanliness: Raw materials must be free from contaminants such as plastics, metals, or other impurities. For recycled paper, additional care is taken to remove any residual inks, adhesives, and other materials that could affect the quality of the paper.
- Fiber Quality: The length, strength, and consistency of fibers are tested to ensure they meet the requirements for producing soft, strong, and durable toilet paper.
2. Pulping Stage Quality Control
Once the raw materials are sourced, they undergo a pulping process to create a slurry of fibers. At this stage, QC focuses on:
- Consistency of the Pulp: The pulp consistency is monitored to ensure uniformity in thickness and texture, which is critical for producing high-quality toilet paper.
- De-inking (for Recycled Paper): For recycled materials, de-inking is performed to ensure that all ink and contaminants are effectively removed. The cleanliness of the pulp is critical to prevent any residual inks or chemicals from affecting the softness and appearance of the final product.
3. Sheet Formation and Drying
The next step is the formation of paper sheets. This is where the pulp slurry is spread over a mesh screen, and the water is drained to create a wet mat of fibers. Quality control at this stage involves:
- Uniformity of the Paper: The paper’s thickness, texture, and strength must be consistent. Variations in thickness can lead to weak areas in the paper, which may tear easily or not absorb well.
- Even Drying: The wet mat is passed over heated cylinders to dry. It’s essential that the drying process is uniform to avoid issues like wrinkles, warping, or irregular texture that could impact the softness and usability of the toilet paper.
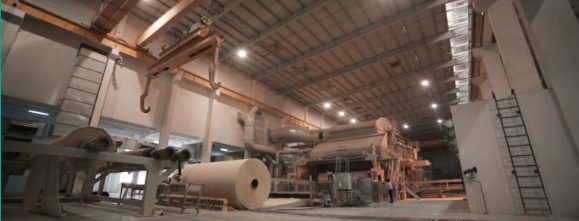
4. Embossing and Perforation Checks
Embossing adds texture to the paper and enhances its softness. Perforation makes the paper easy to tear into individual sheets. Quality control measures during this stage include:
- Embossing Pattern Consistency: The embossing pattern must be consistent across the entire batch of paper. A high-quality embossing process results in a smoother texture that enhances the paper’s comfort and strength.
- Perforation Alignment and Strength: The perforations should be aligned precisely to ensure that consumers can easily tear the sheets without difficulty. The strength of the perforations is also monitored to avoid tearing too easily while maintaining the paper’s overall integrity.
5. Cutting and Packaging
Once the paper is embossed and perforated, it is cut into rolls and packaged. Key QC checks during this phase include:
- Roll Consistency: Each roll must meet the correct dimensions (diameter and length), and the weight of the roll must be consistent. Variations can affect the consumer’s experience and packaging efficiency.
- Packaging Integrity: The wrapping materials must be strong and clean to protect the rolls from contamination. The packaging must also meet industry standards for appearance and safety.
6. Softness, Strength, and Absorbency Testing
These three physical characteristics are essential for toilet paper to perform effectively. Quality control ensures that the paper meets the necessary standards by conducting tests such as:
- Softness Testing: The softness of toilet paper is evaluated through various methods, such as tactile tests or mechanical instruments like the Handle-O-Meter. Softness is a critical factor for consumer satisfaction.
- Strength Testing: The toilet paper is tested for both dry and wet strength to ensure it holds up under use. Tests such as tensile strength and burst strength are conducted to verify that the paper won’t tear too easily.
- Absorbency Testing: Toilet paper is tested for its ability to absorb moisture efficiently. This is done by placing the paper in water and measuring the time it takes to absorb moisture and the amount of moisture the paper can hold.
7. Hygiene and Safety Standards
Since toilet paper is a hygiene product, maintaining cleanliness is a top priority. Quality control ensures that the product adheres to strict safety standards:
- Microbial Testing: Toilet paper samples are tested for bacteria, fungi, and other pathogens to ensure they are safe for consumer use.
- Chemical Residue Testing: It’s essential to ensure that no harmful chemical residues, such as bleach or dyes, remain on the final product. Testing ensures that the toilet paper is safe for skin contact and does not contain any harmful substances.
8. Final Inspection and Sampling
Before the toilet paper rolls are shipped out to stores, a final inspection is conducted. This includes:
- Visual Inspection: A thorough visual inspection checks for defects such as holes, tears, or discoloration.
- Random Sampling: A random selection of rolls from each batch is tested for softness, strength, and absorbency to ensure that the final product is consistent and meets the required standards.

Key Considerations for Choosing the Right Toilet Paper Manufacturer
This chart will help guide your decision-making when selecting the right toilet paper manufacturer that aligns with your quality, sustainability, and business needs.
Key Consideration | Explanation |
Product Quality | Ensure the manufacturer consistently produces high-quality toilet paper that meets softness, strength, and absorbency standards. |
Raw Material Sourcing | Check if the manufacturer uses high-quality raw materials (e.g., virgin pulp, recycled fibers) that are safe and sustainable. |
Environmental Practices | Assess the manufacturer’s commitment to eco-friendly practices, such as sustainable sourcing, recycling, and energy efficiency. |
Production Capacity | Verify if the manufacturer has the capacity to meet your demand, whether for small or large-scale orders. |
Certifications and Standards | Look for certifications like FSC (Forest Stewardship Council) or EcoLabel to ensure the manufacturer adheres to industry standards. |
Customization Options | Consider if the manufacturer offers customizable features (e.g., embossed patterns, packaging options, or private labeling). |
Pricing and Cost-Effectiveness | Compare pricing structures to ensure they offer competitive rates without compromising on quality. |
Lead Times and Delivery | Evaluate their ability to meet delivery deadlines and maintain stock availability to avoid delays in your supply chain. |
Customer Service and Support | Choose a manufacturer known for responsive customer service and support to resolve any issues promptly. |
Reliability and Reputation | Look into the manufacturer’s reputation and reliability in the market, including customer reviews and industry feedback. |
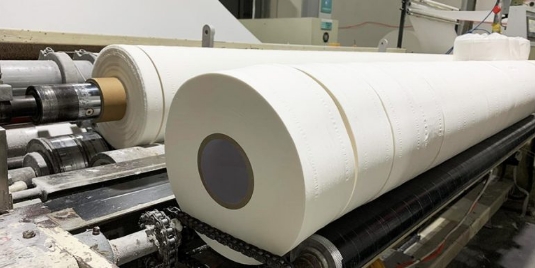
Donsea Paper, established in 2001, is a leading eco-friendly bamboo toilet paper manufacturer. With over 24 years of experience, they offer high-quality, sustainable toilet paper made from 100% bamboo pulp. Donsea Paper is committed to environmental sustainability, holding certifications like FSC, ISO, and BSCI, ensuring adherence to international quality and environmental standards. Donsea Paper provide customizable options through OEM and ODM services, meeting diverse customer needs.
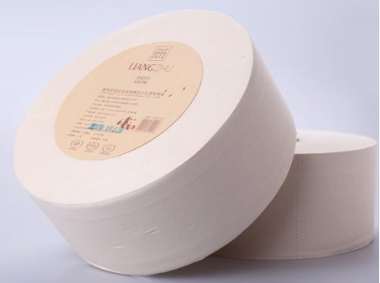
Final Thoughts
Manufacturing toilet paper is a highly technical and carefully managed process that transforms raw fiber materials into a daily necessity. Through pulping, sheet formation, converting and rigorous quality control, manufacturers create a product that balances softness, strength, and convenience. As consumer demands shift toward more sustainable options, manufacturers are also exploring eco-friendly materials and new innovative production methods, shaping the future of toilet paper manufacturing.